burr direction in sheet metal Burrs are especially common in sheet metal operations such as punching, laser cutting, and shearing. The force used to cut or shape metal sheets can cause the material to be displaced, resulting in burrs. Even refining or finishing . Hager Ashley J501 16 Amp Junction Box 4 Terminal. The J501 is specially designed for use with lighting circuits, ideal for installing downlights efficiently and safely.
0 · metal burr removal
1 · mechanical burr
2 · how to deburring a burr
3 · deburring metal burr
4 · burr on metal barrel
5 · burr on metal
6 · burr in metal manufacturing
7 · acceptable burr height for metal
Ikea used to make these boxes that were made out of 1/4" plywood connected with 8 galvanized metal brackets that had an extra lip on the top that helped keep the box together. I wanted to use the same method for making some boxes but I can't seem to find these kinds of brackets (pictured) anywhere.
The maximum acceptable burr height for a metal stamping is equal to 10 percent of sheetmetal thickness. The above statement would be true if all stampings were produced from low-carbon steel less than 0.050 in. thick, .A burr is a raised edge or small piece of material that remains attached to a workpiece after a modification process. It is usually an unwanted piece of material and is removed with a deburring tool in a process called deburring. Burrs are most commonly created by machining operations, such as grinding, drilling, milling, engraving or turning. It may be present in the form of a fine wire .Burr allowance is generally 10% of the thickness of the sheet material. To minimize instances and severity of burrs, avoid sharp corners and complex cutouts when possible. When such factors .
Burrs are especially common in sheet metal operations such as punching, laser cutting, and shearing. The force used to cut or shape metal sheets can cause the material to be displaced, resulting in burrs. Even refining or finishing .
Burrs are formed during processes such as face milling and drilling by the tool angle as it works on the part. The size and type of the burr and its direction will depend on the machine and process used.Burr formation is common sheet metal defect and Burr control / deburring is an important issue for industrialist and engineers. It is produced in all shearing & cutting operations. In sheet metal . They include burrs, fracture, burnishing, rollover, and work hardening. A burr, or protruding ragged edge, shown at 100x magnification, occurs as the material is sheared at an angle against the blanking direction. .
In the context of metal manufacturing, a burr refers to the formation of rough edges or ridges on the metal piece. The reason behind it lies in the manufacturing process and the tools involved in its production. It is especially common with cutting operations on sheet metal. The maximum acceptable burr height for a metal stamping is equal to 10 percent of sheetmetal thickness. The above statement would be true if all stampings were produced from low-carbon steel less than 0.050 in. thick, using typical punch-to-die cutting clearances. (3) Wisely choose the direction: Based on the corner effect of burrs, during metal cutting, the outlet should be located at the part with a large corner angle to reduce burr formation. At the same time, it’s important to note that the cutting edge should be located in a place where removing burrs is easy, to reduce the cost of removing them.A burr is a raised edge or small piece of material that remains attached to a workpiece after a modification process. [1] It is usually an unwanted piece of material and is removed with a deburring tool in a process called deburring .
Burr allowance is generally 10% of the thickness of the sheet material. To minimize instances and severity of burrs, avoid sharp corners and complex cutouts when possible. When such factors cannot be avoided, be sure to note burr direction in your design so they can be taken into account during stamping (See the “Stamped Edges” image below).
metal burr removal
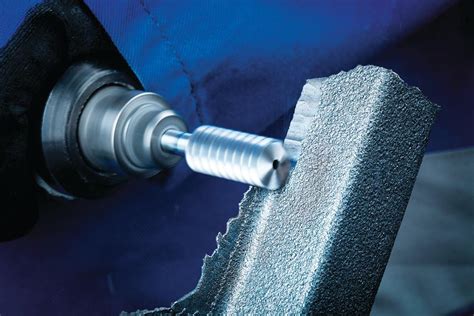
Burrs are especially common in sheet metal operations such as punching, laser cutting, and shearing. The force used to cut or shape metal sheets can cause the material to be displaced, resulting in burrs. Even refining or finishing processes, such as grinding, can introduce burrs. Burrs are formed during processes such as face milling and drilling by the tool angle as it works on the part. The size and type of the burr and its direction will depend on the machine and process used.
lt ga metal framed field fabricated metal door canopy
Burr formation is common sheet metal defect and Burr control / deburring is an important issue for industrialist and engineers. It is produced in all shearing & cutting operations. In sheet metal parts burr is usual but after a specified limit it takes a form of defect. This leads to rework and quality problem of part. They include burrs, fracture, burnishing, rollover, and work hardening. A burr, or protruding ragged edge, shown at 100x magnification, occurs as the material is sheared at an angle against the blanking direction. Burrs can interfere with subsequent forming processes. Five standard burr classes have been developed that help specify burr size, how they were formed and difficulty of removal. Brushing is a common deburring solution, and newer technology is contributing to longer overall brush life.
In the context of metal manufacturing, a burr refers to the formation of rough edges or ridges on the metal piece. The reason behind it lies in the manufacturing process and the tools involved in its production. It is especially common with cutting operations on sheet metal. The maximum acceptable burr height for a metal stamping is equal to 10 percent of sheetmetal thickness. The above statement would be true if all stampings were produced from low-carbon steel less than 0.050 in. thick, using typical punch-to-die cutting clearances. (3) Wisely choose the direction: Based on the corner effect of burrs, during metal cutting, the outlet should be located at the part with a large corner angle to reduce burr formation. At the same time, it’s important to note that the cutting edge should be located in a place where removing burrs is easy, to reduce the cost of removing them.
mechanical burr
A burr is a raised edge or small piece of material that remains attached to a workpiece after a modification process. [1] It is usually an unwanted piece of material and is removed with a deburring tool in a process called deburring .Burr allowance is generally 10% of the thickness of the sheet material. To minimize instances and severity of burrs, avoid sharp corners and complex cutouts when possible. When such factors cannot be avoided, be sure to note burr direction in your design so they can be taken into account during stamping (See the “Stamped Edges” image below).
Burrs are especially common in sheet metal operations such as punching, laser cutting, and shearing. The force used to cut or shape metal sheets can cause the material to be displaced, resulting in burrs. Even refining or finishing processes, such as grinding, can introduce burrs. Burrs are formed during processes such as face milling and drilling by the tool angle as it works on the part. The size and type of the burr and its direction will depend on the machine and process used.
Burr formation is common sheet metal defect and Burr control / deburring is an important issue for industrialist and engineers. It is produced in all shearing & cutting operations. In sheet metal parts burr is usual but after a specified limit it takes a form of defect. This leads to rework and quality problem of part.
They include burrs, fracture, burnishing, rollover, and work hardening. A burr, or protruding ragged edge, shown at 100x magnification, occurs as the material is sheared at an angle against the blanking direction. Burrs can interfere with subsequent forming processes.

how to deburring a burr


lt distribution box hs code
lpr metal fabrication servicing
Fabricated Metals manufactures only heavy duty enclosures that provide the strength and durability using 12 GA steel and aluminum in our enclosures. Flexibility is also accounted for and built into every outdoor stationary battery cabinet as industry standards and regulations change at .
burr direction in sheet metal|acceptable burr height for metal