spot welding sheet metal thickness The depth of depression on the sheet surfaces caused by welding electrodes should never exceed 25 percent of the sheet metal thickness. . Watson Metals Co. can handle all of your commercial and residential metal fabrication needs in Surry and Wilkes County. Call 336-366-4500 for more details.
0 · what is spot welding
1 · spot welding temperature chart
2 · spot welding resistance chart
3 · spot welding machine specifications
4 · sheet metal welding depth chart
5 · process parameters for spot welding
6 · metal spot welding techniques
7 · how to calculate spot welding
$131.99
horrizontall sheet metal stick welds
Metal thicknesses represent the actual thickness of the sheets being welded. In the case of welding two sheets of different thicknesses, use the welding parameters for the thinner sheet. Welding parameters are applicable when . The depth of depression on the sheet surfaces caused by welding electrodes should never exceed 25 percent of the sheet metal thickness. .
Unlock the secrets of spot welding with our comprehensive guide. Learn techniques, safety measures, and more. Perfect your welding skills today! Spot weldments are best when welding material 0.20”-0.90” thick. Materials thicker than 0.90” aren’t suitable for a spot weld because the .Spot welding (also known as resistance spot welding) is a resistance welding process. This welding process is used primarily for welding two or more metal sheets together by applying pressure and heat from an electric current to the .Resistance spot welding is done correctly when we meet the result of nugget diameter. Weld must have a nugget diameter of 5*√t. Where “t” is thickness of sheets being weld. For explanation, in spot welding we weld two sheets. Both .
horizontal cnc milling machine
Spot welding is a resistance welding method widely used to join sheet metal in the automotive, battery, and auto-body industries. Instead of an arc, this method uses pressure and heat to form small welds in the form of a spot or nugget. Resistance Spot Welding. Supersedes ANSI/AWS D8.7-88R. Prepared by AWS D8 Committee on Automotive Welding. Under the Direction of AWS Technical Activities . Spot welding is used to join electricity-conducting sheet metal and wire meshes. Its typically used to weld thin metals but thicknesses above 1 in. are possible only with specialized heavy-duty equipment.Typically the sheets are in the 0.5 to 3 mm (0.020 to 0.118 in) thickness range. Forcing a large current through the spot will melt the metal and form the weld. The attractive feature of spot welding is that a large amount of energy can be .
A portable spot welder. Spot welding (or resistance spot welding [1]) is a type of electric resistance welding used to weld various sheet metal products, through a process in which contacting metal surface points are joined by the heat . Welding sheet metal often requires a beautiful, smooth weld line. You can only achieve that naturally with a TIG welder. . (0.001) inch of thickness for thin carbon steel. Stainless steel requires 1/3 fewer amps, and aluminum .
Spot Welding. Also known as resistance welding, spot welding involves compressing two pieces of sheet metal and applying pressure and heat from copper electrodes to create a nugget of weld that connects the pieces. . Spot welding is capable of joining almost any metal & alloy sheet with a maximum thickness of 3mm. In the current scenario, a wide range of industries uses automated & semi-automated spot welding, including automotive, aerospace, kitchenware, architecture, electrical, and construction.on-line quality monitoring and controlling of resistance spot welding [19]. Attention is paid to the spot welds behavior under conditions of fatigue [20]. According to CSN EN ISO 4063 the resistance welding falls into spot welding (resistance spot welding, method 21) and seam welding (resistance seam welding, method 22). Imagine a welding process that minimizes distortion, enhances precision, and improves efficiency. Laser welding technology for sheet metal does exactly that, revolutionizing industries from automotive to high-tech electronics. This article explores the advantages of laser welding over traditional methods, detailing its superior heat control, speed, and flexibility. .
Spot welding is commonly used to weld sheet metal. It’s a straightforward process, but there are many ways that things can go wrong if you don’t have spot welding experience. This article will teach you the basics of the spot welding process and how it works, typical applications, suitable materials, and common problems you may encounter.Resistance spot welding (RSW) process is widely used in sheet metal joining process due to its high speed, suitability for automation and inclusion in high-production assembly lines with other fabricating operations. It is a complex process in which coupled interactions exist between electrical, thermal, mechanical, metallurgical phenomena, and
Spot-Welding Sequences on Sheet Metal Distortion Enkhsaikhan Boldsaikhan 1,* , Michael Milhon 1, Shintaro Fukada 2, Mitsuo Fujimoto 2 and Kenichi Kamimuki 3 . a nominal thickness of 2 mm (0.08 inch) and a 2029-T8 aluminum alloy (AA2029-T8) with a nominal thickness of 3 mm (0.12 inch). The mechanical properties of the sheet metals are
You want to weld the same thickness of metal. Always coat the work piece with a flux before welding to prevent any unwanted deposits from forming. Clean your work piece with a degreaser or brake cleaner after welding. Spot Welding Sheet Metal with MIG Welder. A MIG welder is a great all-around welder when welding sheet metal. Microhardness tests show that DP600 GI samples have the highest hardness, about 420 HV in weld nugget and 250 HV in base metal, followed by TRIP600-bare, about 400 HV in weld nugget and 220 HV in . Spot welding is a great way to join two pieces of sheet metal together quickly and easily. With the right equipment and technique, anyone can learn how to spot weld quickly and efficiently! Remember to wear proper safety gear when working with electricity or hot metals—your safety should always be your top priority when tackling any new project! The joining of metal sheets in a variety of industries, such as the automobile, aerospace, and electronics, is frequently accomplished by spot welding. Due to the special characteristics of aluminum, there are particular difficulties and considerations while spot welding aluminum sheets. . The thickness of the sheet and the characteristics of .
One general criterion of resistance spot-welding is that the weld shall have a nugget diameter of 5*t 1/2, “t” being the thickness of the steel sheet. Thus, a spot weld made in two sheets, each 1 mm in thickness, would generate a nugget 5 mm in diameter according to the 5*t ½-rule. Diameter of the electrode contact surface should be .This method will avoid more heat energy, and provide good aesthetic spot weld. Strength can be the factor you need to consider here. By multiplying the thickness of the sheet by 10, a best value for weld time can be calculated. When welding .The process of spot welding sheet metal fabrications is quite simple it is basically harnessing the heat generated by the resistance to electrical current flow at the interface/joint of two separate pieces of sheet metal. At V&F Sheet Metal we .
For spot welding of two steel sheets (base metal) each of 3 mm thickness, welding current of 10000 A is applied for 0.2 seconds. The heat dissipated to the base metal is 1000 J. Assuming that the heat required for melting 1 mm 3 volume of steel is 20 J and interfacial contact resistance between sheets is 0.0002 Ω, the volume (in mm 3) of weld nugget is _____ Analysis of the Welding Deformation of Resistance Spot Welding for Sheet Metal with Unequal Thickness January 2010 Journal of Solid Mechanics and Materials Engineering 4(8):1214-1222
Resistance spot welding is the dominant process for joining sheet metals in automotive industry. Even-thickness combinations are rarely used in practice; therefore, there is clearly a practical . Then a final weld sequence forms the nugget. This technique works best for sheet metal to 12 gauge. Pulsation: This sequence, typically used for sheet metal 11 gauge and thicker, employs a series of heat/cool impulses to move the coating out of .Generally, the pressure depth on the sheet surfaces should always be at most 25 percent of the sheet metal thickness. Squeeze Time In Spot Welding. . mean lower costs. Overall, spot welding equipment is relatively cheap, especially compared to other methods used in sheet metal welding. The drawbacks of Spot Welding Are: Limited Weld Desing .
The weldability of spot weld joints of AA5052 aluminium alloy with dissimilar thickness was investigated by Mat Din et al. [48] One sheet had a constant thickness of 2 mm and the other sheet . The key thing when buying a spot welder is understanding the thickness of sheet metal you want to weld. Spot welders are best suited for thin sheet metal. Squeeze type spot welding would typically be able to weld sheets from 0.5 to 3mm (0.020 to 0.118 in) thickness. With hand held models handling up to 2 sheets of 16ga.
what is spot welding
Aerospace Industry (sheet metal assemblies) – Spot resistance welding is utilized in the aerospace industry for joining sheet metal components, creating strong and lightweight structures for aircraft. 6. . Thickness Limitations – Resistance welding is effective for thin to medium-thickness materials. However, it may face challenges when .which was the precursor to resistance spot welding process. The square-root based . extremes of sheet thickness. For example, at a thickness of 0.1 mm, the nugget diameter required is 1.26 mm, which is 12.6 times the sheet thickness, which is huge; while at . Competition between weld strength and base metal strength can be setup for the two .4500.01 Introduction to Spot Welding ♦ Suitability of aluminium and its alloys for spot welding ♦ Comparison of physical properties of aluminium and unalloyed steel ♦ Resistances during spot welding of steel and aluminium ♦ Constitution of the oxide film ♦ Surface pretreatment ♦ Contact resistance after surface pretreatment
VEVOR Portable Spot Welder, 1/8-inch Spot Welder Machine with 1.5KVA Input Capacity, Handheld Welding Tip Gun, Metal Sheet Spot Welding Machine for Aluminum Sheet, Carbon Steel - Amazon.com. . and has a long service life. It provides perfect weld for materials that have a thickness, ensuring the stability and reliability of your welding work.
spot welding temperature chart
spot welding resistance chart
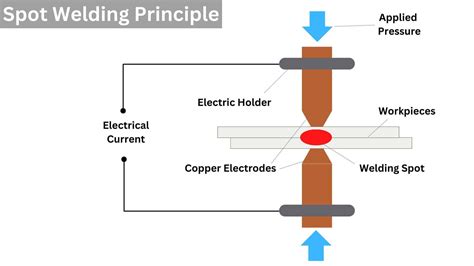
I've run across a furnace that has no junction box, and saw nothing special in the instructions. The pigtails to splice to are just free in the larger wiring area with lots of internal .
spot welding sheet metal thickness|spot welding temperature chart